
I should have done the same on the intermediate panels, but "too soon old too late smart". It made cutting the sheets a piece of cake, and I had lots of sheet left over. I used the thin cardboard from an old file folder.
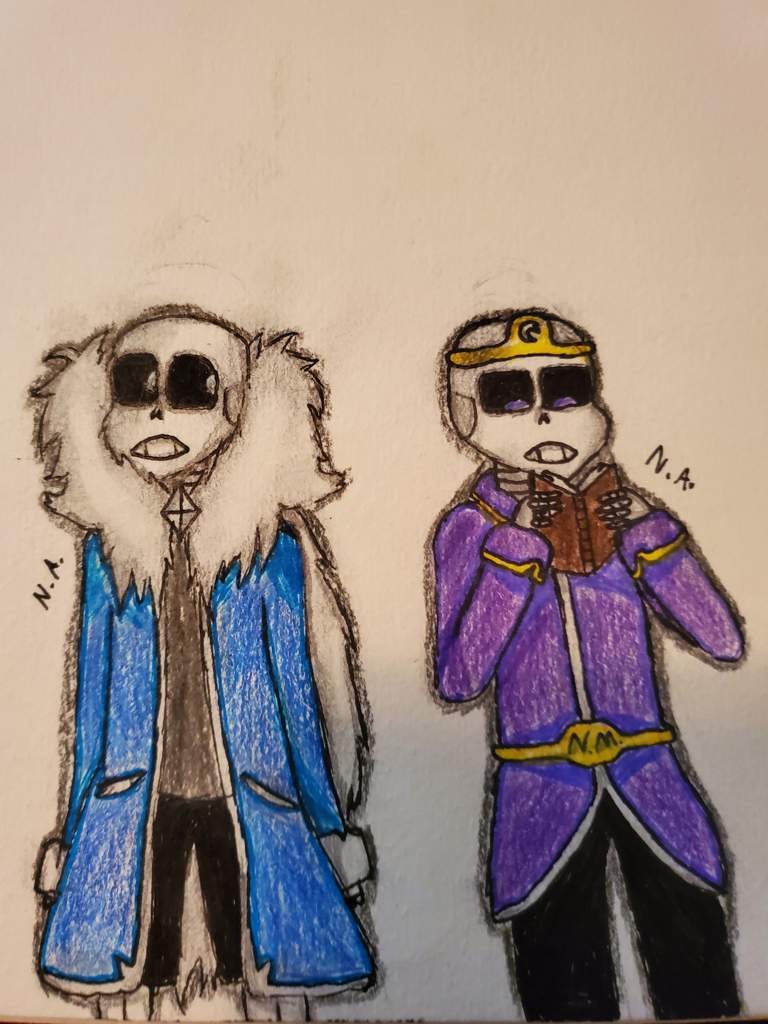
Anyway, they come out pretty equivalent: nearly the same weight, and very light overall.įor the X-RES, here is a tip to easier work: make a template for the top and bottom sheets. Every part is provided for the X-Dream, while the X-RES requires cutting parts from sheet. The X-Dream is definitely easier to build, even though the rib count and overall design is the same. I built an X-RES and an X-Dream tip panel, side by side.
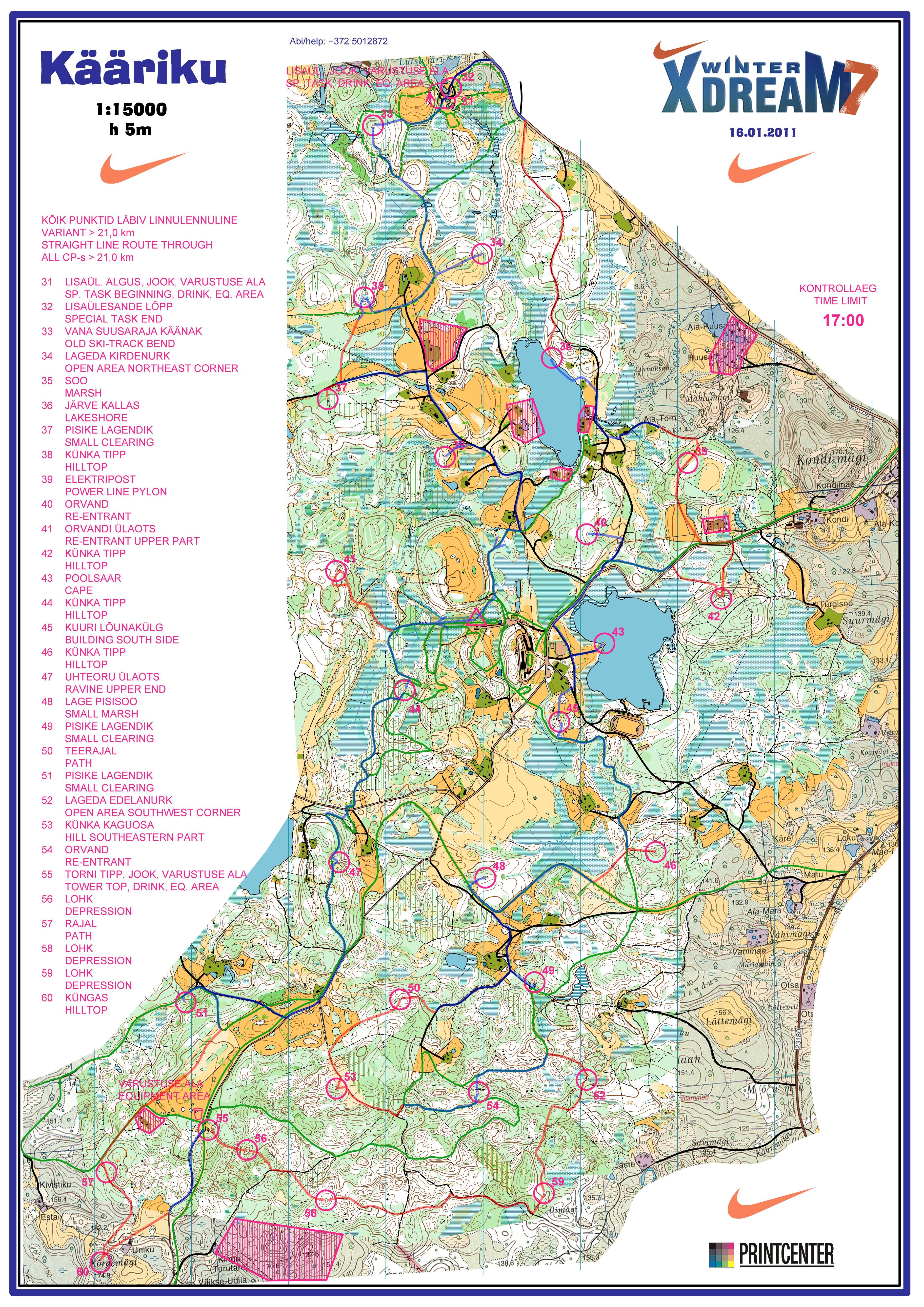
The smoother the balsa is, the better the covering will adhere (and appear!).ĭo that four times in all, and you are done. It is hard to actually remove material with a fine block, but balsa polishes very well. I polished everything all over with the fine block. On the bottom, I sanded the flat portion of the wing to make sure the balsa sheet went smoothly into the spruce spar. Take a few strokes, and look: when you are done, STOP. Any tool marks should disappear, as well as any laser ash. I then continued with the green block: make sure the top sheet blends exactly with the ribs, and that the ribs go smoothly into the trailing edge. I used the edge of the block to sand the hard feet of the plywood ribs. The trailing edge needs to be thinned out, and this will do it. Use the block flat, and let it bear on the trailing edge itself. I used the green block again on the bottom of the wing, sanding the trailing edge to remove all the feet near the aft end of the ribs. Took about three minutes, and when I used the templates, I was done shaping. I used the green block and shaped the leading edge, rounding of the top and bottom surfaces until the flat nose disappeared. You are done when the top and bottom surfaces fair smoothly into the leading edge, and the flat nose is smoothly tapered from root to tip. With practice, you can feel the block cut into the glue line.
XDREAM SATISFIED FULL
Whichever block, I took long strokes over the full span, and moved the block slowly. For a couple of sheets, as this stage became close, I switched to my trusty green sanding block, for better control. There was still a flat front to the leading edge. I just kept it parallel to the adjacent sheet (top or bottom) until the sheet led smoothly into the leading edge. Getting close, I changed to a very aggressive block. Four, five or six passes was all it took, top and bottom. I just kept the plane parallel to the surface of the sheet adjacent to the leading edge, and took long strokes. I started with a razor plane, and removed leading edge material until I was almost (but not quite!) removing sheeting. These are marked, "B-1" and so forth to B-8. I also brought along the handy shaping templates, just as for the center section. The aggressive blocks and the green block actually remove material for shaping. The razor plane is best for removing large amounts of wood with control. I assembled my tools: razor plane several large and aggressive blocks my trusty, green, 120 grit block and a fine block. I tried the scroll saw, but it was too coarse and I was afraid I'd shake something loose. A razor saw took too long, and I wasn't about to sand the end of a stick that stuck out a half inch or so. I experimented with several techniques, and found my belt sander to be (1) quick) (2) easy and (3) safe - in that I didn't remove too much. I started by removing the excess sheet and spar material that sticks out from each end.

The leading edge material is simply glued in place. The evening before, I removed excess sheet with a razor plane, and smoothed the front of the ribs with a sanding block. You will have to believe me when I say: I did each panel in exactly the same fashion. The panels are different, X-RES to X-Dream, mostly in span, but otherwise part-for-part in assembly and shape. I'm only showing pictures of one (1) panel during the process.
